portfolio enhancement
RESPONDING TO THE
CHANGING NEEDS OF
CARTON CONVERTERS
BOBST ENHANCES THE MOST COMPREHENSIVE RANGE OF FOLDER-GLUERS IN THE FOLDING CARTON MARKET
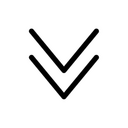
The folding carton industry never stops evolving and shifting, and BOBST, a pioneering force in folding and gluing technology since the 1940s, has recently enhanced its foldergluer equipment portfolio with the introduction of new generation folder-gluers for its EXPERTFOLD, VISION FOLD and NOVAFOLD.
Responding to the changing needs of carton converters in a competitive global market. Bobst continues to lead, by offering one of the most comprehensive folder-gluing lines backed by global service and support. Always responsive to industry trends to ensure accessible performance at every step of production, Bobst invests heavily in research and development, evolving modular production lines and peripherals.
Pierre Binggeli, Head of Product Line Folder-gluers, says, "With our folder-gluer range, we believe in evolution, not revolution. Our expertise is at the heart of our products, which gives folding carton converters around the world confidence in their production capabilities. By continually developing and advancing our machines with new devices and innovations, we're ensuring our customers can always respond to market needs with agility and speed."
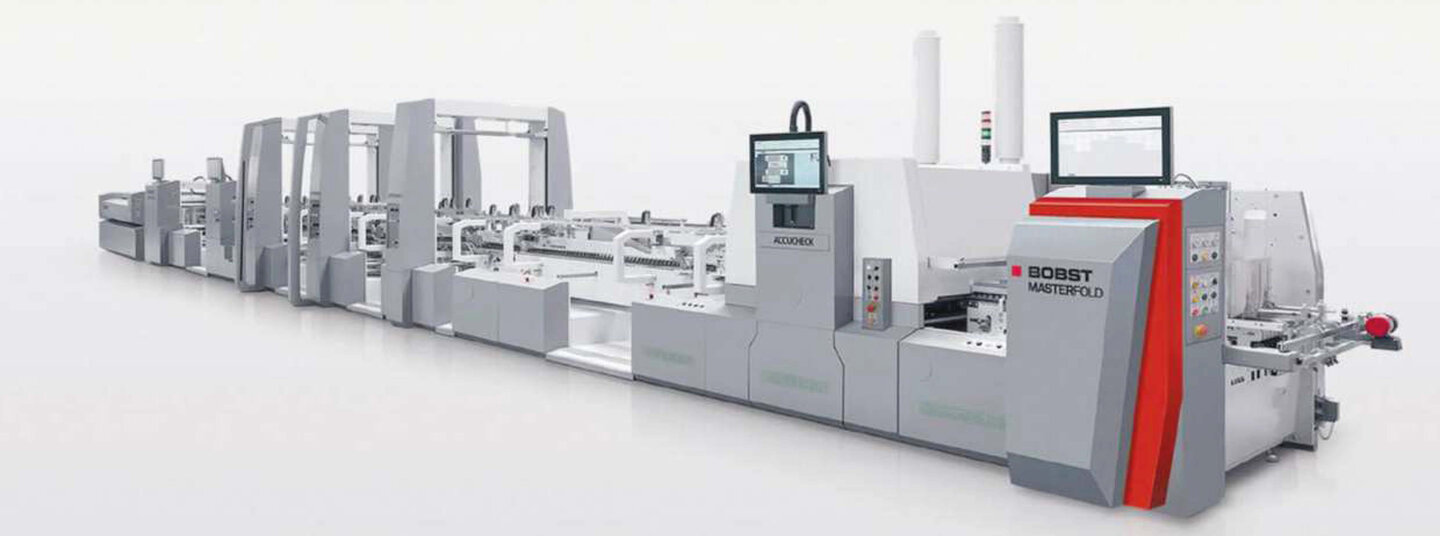

Tailored to market demand
The experience and insight of Bobst are evident in its folder-gluer range. At the core of the portfolio is versatility: the modular design of the machines allows converters to have a tool which meets their current production needs, with the option to modify the configuration for future requirements and ensure the perennity of their investment. Moreover, peripherals such as EASYFEEDER/BATCH INVERTER at the front of the machine or HANDY PACK and CARTON PACK 4 at the delivery, can transform each machine into a complete, high-performance folding-gluing production line.
From the folder-gluer portfolio, customers can choose between the quality and reliability of the NOVAFOLD, the all-rounder VISION FOLD, the high-efficiency EXPERTFOLD or the unique performance of a MASTERFOLD. These machines cover the needs of small- and mid-sized businesses seeking market opportunities to companies with huge converting facilities. Converting different types of packaging, from simple boxes to highly intricate designs, in various sizes: Bobst ensures the availability of a folder-gluer configuration for every application, ensuring that exceptional packaging quality is not a question of chance.
Expertfold and Masterfold machines can be equipped with the zero-fault ACCUCHECK lnline quality control system, the SPEEDWAVE device to boost the production of crash-lock bottom boxes and the GYROBOX, the box-rotating module which allows the production of complex boxes in one go. For full pharma box compliancy, the ACCUBRAILLE unit can be fitted onto the Expertfold and the NICK BREAKER on Masterfold allows in-line breaking of nicks in complex box designs.
Designed with the Bobst Vision of digitisation, automation, connectivity and sustainability, significant recent updates have added new levels of performance to Expertfold, Visionfold and Novafold machines. Adding the SPHERE to all three foldergluers has increased their digital capabilities. The now illimited access to the Bobst Connect functions will lead to a full connectivity over the converting workflow and data accessibility, providing converters with unparalleled visibility over their machines and production.
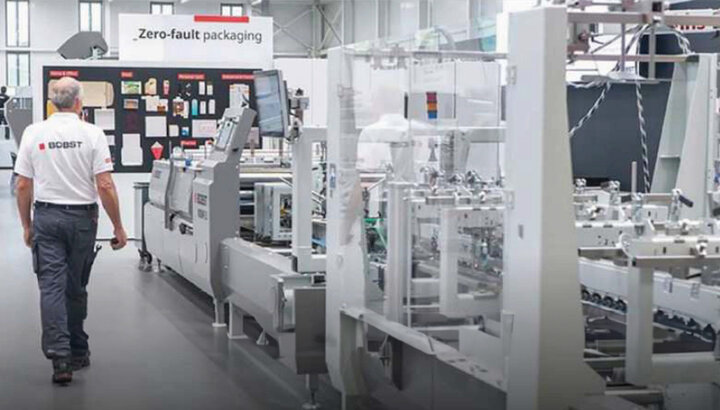
Designed with the Bobst Vision of digitisation, automation, connectivity and sustainability, significant recent updates have added new levels of performance to Expertfold, Visionfold and Novafold machines.
Sustainability at the Core
Sustainable products and processes play a crucial role in folding carton box production today. With ever-increasing demands from consumers and regulatory bodies, and in turn brand owners, sustainability has a vital point of focus.
Limiting the use of resources to a minimum is one way of reducing the ecological impact. However, making sure that blanks become boxes and not waste is also an important part of a cost-efficient production. Apart from keeping brand owners happy with the quality of their packaging, the outstanding precision and quality control devices on the Bobst foldergluers contribute to do just that.
Precise blank aligning and steady transport avoid machine jams, ensuring maximum uptime. Quality checks on AccuCheck can be calibrated to specific customer quality standards, avoiding excessive box ejection. By gradually connecting machines, equipment and people via Bobst Connect and providing precise production data with reports, converters have the possibility to continually improve their production workflow and output. This will help to make their business more profitable and contribute to reduce the ecological footprint of their activities.
In a market where competition is extended from finding potential customers to recruiting qualified workforce, the sustainability of the work environment has also become an issue. Again, the continuous technical development of the folder-gluer line creates a win-win situation. The pneumatic feeder ramps which were recently added to the Expertfold reduce operator workload and setup times by 20%.
Boosting box production and making machine operating less physically challenging can go hand in hand, and allow a new generation of operators to evolve in an increasingly modern industrial environment. Speedy setups and top production speeds thanks to operator-friendly machines and automated processes are therefore a priority in the evolution of the folder-gluer portfolio.
Binggeli concludes, “Our solutions are based around the four key pillars that drive the Bobst Industry Vision. We want to shape the future of the packaging world, providing increased automation for higher productivity, optimised digitalization and connectivity to create interlinked and effective solutions, and put the focus on sustainability, to reduce waste and increase resource efficiency.”
read more
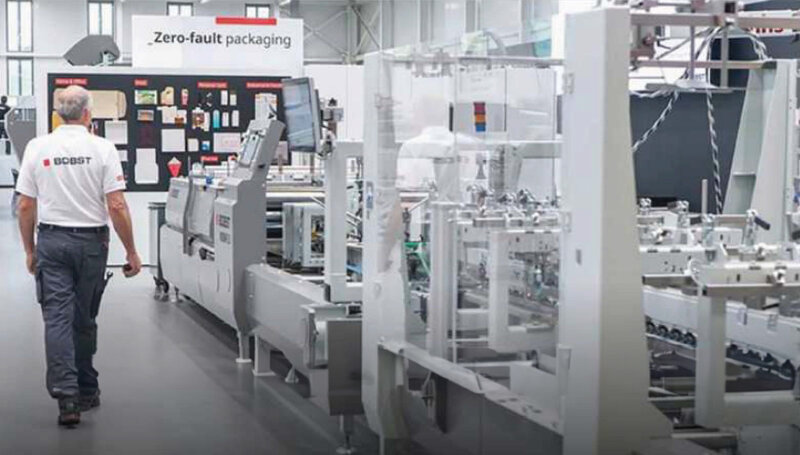
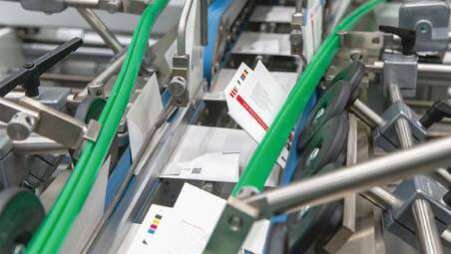
Qualvis ready for drupa machine delivery
Fresh from the manufacturing line at Koenig & Bauer Duran, a new Omega Alius 90 folder gluer shown at drupa is on the next leg of its journey to a new home in Leicester, UK. Along with a brand new Rapida 106 press, the Omega Alius 90 folder gluer is part of a major investment by Qualvis Print & Packaging.
Qualvis already operates a seven-colour Rapida 106 with twin coaters and an lberica cutter creaser. However, the new configuration has been described as something 'entirely different'. It will meet a real need in the market. according to insiders, but will remain undisclosed for competitive advantage.
"All I can reveal about the new press is that it is quite special. Our product designers have worked closely with Qualvis, under strict non-disclosure, to develop a one-of-its-kind capability that will give Qualvis a jump on the market." said Chris Scully, Managing Director, Koenig & Bauer UK.
In a statement from the Joint Managing Directors of Qualvis,
Lisa Smith and Marcus Short, they said, "We're excited to be
installing a special Koenig & Bauer press configuration, it has
been a true collaboration to get to this point and we can't wait to
showcase our new offering. Koenig & Bauer truly aligns with our ethos of innovation and is looking to push the market forward in both sustainability and printing effects."
They continued, "Not only have we partnered with K&B for our new press but we'll also be installing the new Omega Alius 90 folder gluer coming direct from drupa. The first of the new model to market will offer high speeds and intelligent automatic setup. This new folder gluer complements our requirements perfectly. These purchases complement the recent
investment strategy started two years ago, that includes not only
machines, but technology and a solar energy investment to further reduce our carbon footprint. This completes phase two of our longterm investment programme and allows us to continue to focus on sustainable cutting-edge innovation and first-to-market solutions, which is our passion, whilst increasing
capacity to allow for growth which has been exponential over recent years. Extremely exciting times."
"Qualvis make it very for customers to do the right thing in terms of sustainable packaging. From organic vegetable inks to board supply and recycled and recyclable plant-based materials, their whole packaging production is vegan friendly," adds Scully. "At Koenig & Bauer, one of our main strengths is our ability to
innovate and develop technology on a project-by-project basis. We're pleased that they chose us to be their innovation partner on this project."
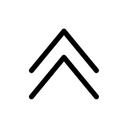
back to top